Safety
Occupational Safety and Health
Safety is a top management priority for the Kaneka Group, and it is our social mission to improve safety. To ensure safe and secure operations, we believe it is important to create a workplace environment where employees can work in good physical and mental health.
Preventing Occupational Accidents
Kaneka Group has set out Zero Accident Principles, requiring every employee to follow them without exception and to act in ways that build a strong safety culture.
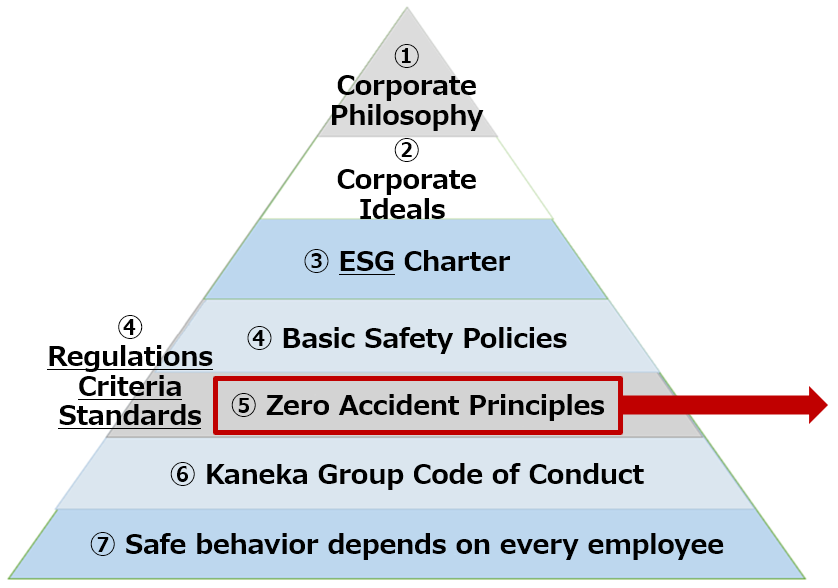
Zero Accident Principles
- All people, you and me, are indispensable
We ensure everyone is working safely.
[Pledge of zero accidents] - Safety is everyone’s responsibility
We do not miss sparing the time to seek safety.
[Participation in safety] - There is no trick to safety
We always value a fundamental approach to it.
[Adherence to safety basics] - Be aware of potential danger
We endeavor to eliminate safety risks
[Safety in advance] - Where there is carelessness, there is the possibility of an accident
We do not allow even a small chance of negligence.
[99%, yet 0%]
ESG safety and quality inspections confirm the status of on-site safety management at manufacturing sites and the implementation of safety activities based on the key policies of the Safety Committee. Areas requiring improvement are shared between the head offices and manufacturing sites. We draft improvement plans with a one-year timeframe and implement PDCA cycles throughout the year.
In 2023, occupational accidents frequently occurred due to insufficient safety awareness, with the number of incidents remaining flat over the past three years. Kaneka Group’s accident frequency rate worsened by 0.07 points year on year to 0.42. However, the accident severity rate improved by 0.01 points due to a decrease in the number of serious accidents. We will continue to enhance each employee’s safety awareness and prevent occupational accidents by advancing safety activities that adhere to the Zero Accident Principles, such as improving risk sensitivity and ensuring equipment safety.
Accidents Resulting / Not Resulting in Lost Time
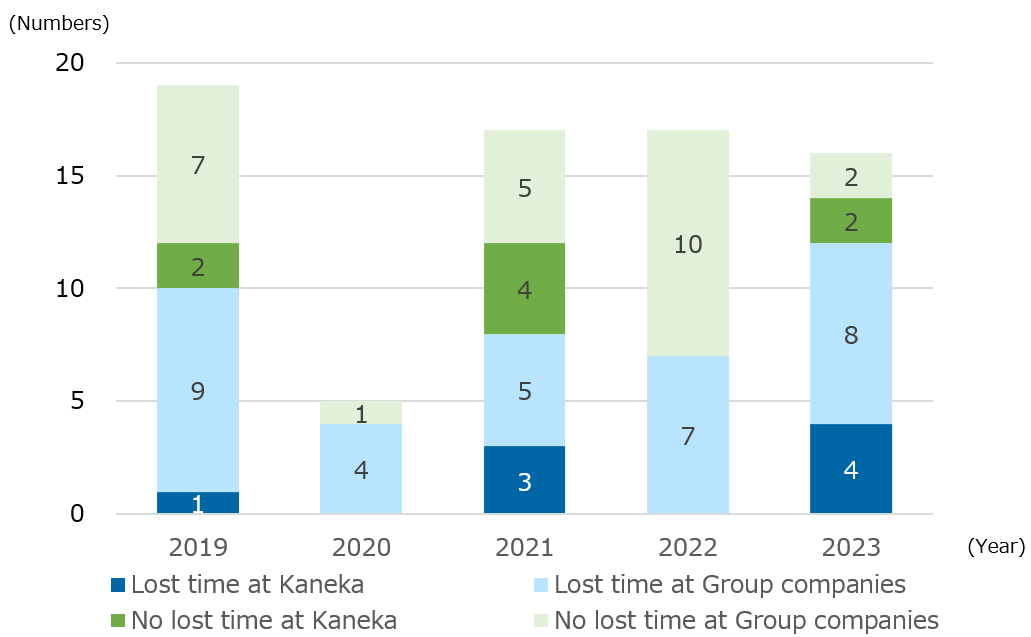
Note: The number of occupational accidents includes those among employees at Kaneka and partner companies working in the Kaneka Group.
Accident Frequency Rate
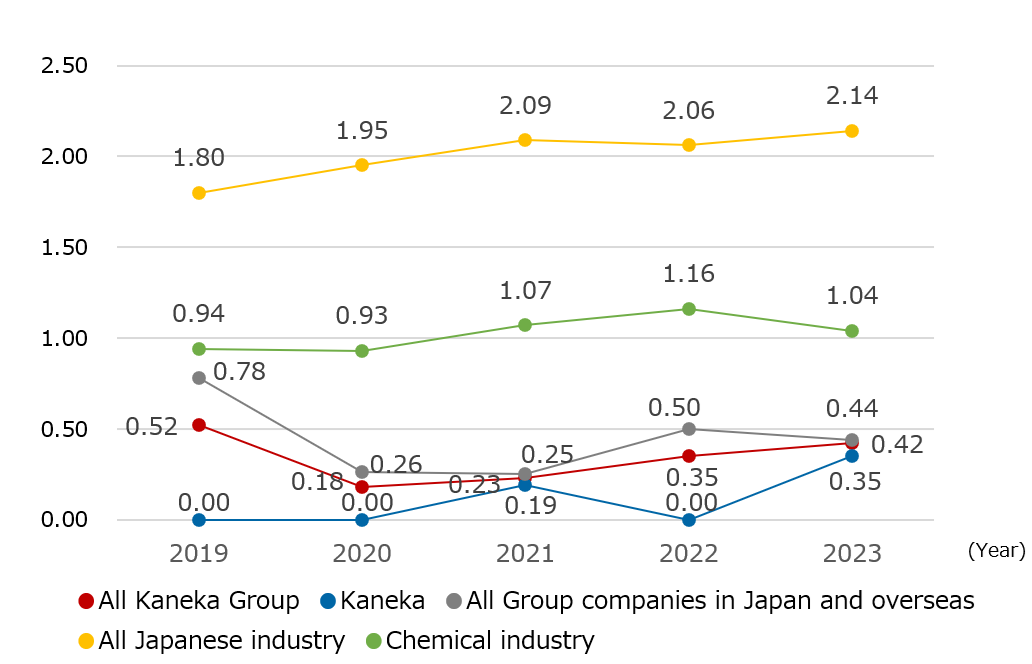
Accident Frequency Rate : An indicator that shows the frequency of occupational accidents that caused death and/or injury by indicating the number of casualties per total 1 million actual working hours.
Scope:Includes manufacturing sites with regular employees, contract employees, and temporary employees dispatched from other companies. The Tomatoh (Hokkaido) Manufacturing Site, completed in August 2024, is not included in 2023 results. Employees seconded to or from other companies and employees of partner companies are not included.
Accident Severity Rate
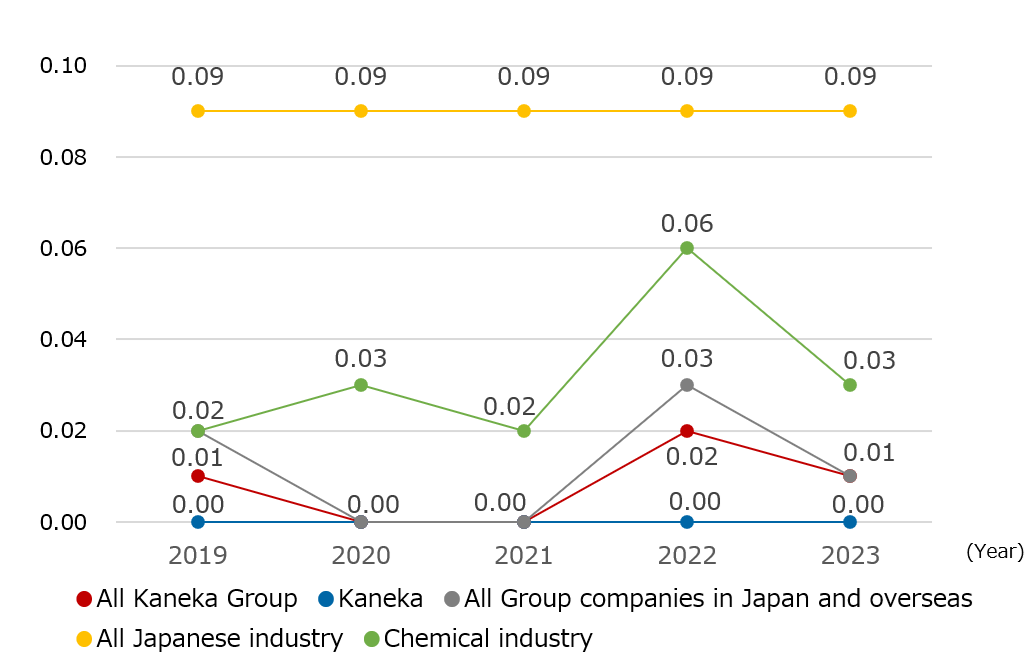
Accident Severity Rate :An indicator that shows the level of severity of occupational accidents by indicating the number of lost work days per total 1,000 working hours. The number of lost work days is calculated as equivalent to the number of days lost from work due to an accident resulting in work absence.
Scope:Includes manufacturing sites with regular employees, contract employees, and temporary employees dispatched from other companies. The Tomatoh (Hokkaido) Manufacturing Site, completed in August 2024, is not included in 2023 results. Employees seconded to or from other companies and employees of partner companies are not included.
Enhancing Our Occupational Safety and Health Management System
Our all parent manufacturing sites acquired Occupational Safety and Health Management System (OSHMS) certification from the Japan Industrial Safety & Health Association (JISHA) in fiscal 2007, and have continued our efforts to enhance these systems.
OSHMS Certifications
Manufacturing Site | Location | Certification Date | Certification No. |
---|---|---|---|
Takasago Manufacturing Site | Hyogo | March 10, 2008 | 08-28-13 |
Osaka Manufacturing Site | Osaka | August 21, 2007 | 07-27-10 |
Shiga Manufacturing Site | Shiga | January 15, 2008 | 08-25-6 |
Kashima Manufacturing Site | Ibaraki | December 13, 2010 | 10-8-26 |
Prevention of Slips, Trips, and Falls
Over the past five years (2019 to 2023), the most frequent occupational accidents have been slips and falls and entrapment/entanglement. In recent years, there has been an increasing trend in accidents involving slips and falls. To prevent these, we are focusing on improving the working environment and enhancing the awareness of potential dangers among workers at domestic group companies with a high number of occupational accidents. We are undertaking the following two initiatives.
Improving the Work Environment
- In each company, model areas were designated, and concentrated improvements were made to locations prone to tripping, such as stairs and steps (improvements were made in 134 areas and 216 locations across 50 manufacturing sites).
- The ideal model area will be shared company-wide as a best practice.
Improvement examples
Before improvement | After improvement |
---|---|
![]() |
![]() |
![]() |
![]() |
![]() |
![]() |
Raising awareness of potential hazards
- We use IT tools to measure each person’s physical traits and make their risk of falling visible.
- The program combines measurement, analysis, and targeted exercises to lower fall risk. After a few months, we measure again to check the impact of the exercises and refine the process through a PDCA cycle. This initiative has been rolling out in stages since fiscal 2023.

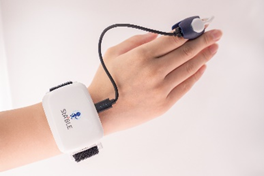
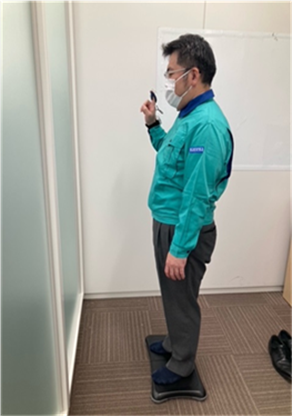
StA2BLE™ is a registered trademark of UNTRACKED Corporation.
(Photo courtesy of UNTRACKED Corporation)
Feeling Danger Physically: Experiential Learning
Kaneka Group is pursuing hands-on learning to enhance sensitivity to risks. In addition to conventional hands-on safety experience equipment, we introduced virtual reality-based learning equipment that allows participants to experience 17 simulation scenarios, including crashes, electric shocks, and explosions. Through this initiative, we are working to increase safety awareness.
In fiscal 2023, 1,510 individuals participated in the training.
Training Safety Technicians
Kaneka is committed to maintaining a safe and secure factory environment by implementing more advanced risk assessments and engineering measures. In fiscal 2023, we launched a new Plant Safety Technology Training program aimed at developing safety engineers capable of addressing these challenges.
In this training program, we provide specialized education in areas such as safety engineering and reliability engineering, with external academics serving as instructors. In fiscal 2023, 20 participants attended the Basic Course, which consisted of seven sessions. In addition, those who completed the Basic Course will have the opportunity to challenge themselves further by enrolling in the more technically specialized Advanced Course starting in fiscal 2024.
Safety training (including training by job level)
The Kaneka Group is continuously engaged in developing safety personnel through various safety education programs, including risk assessment training, safety engineer training, and experiential learning. Additionally, we conduct line manager training for supervisors. In fiscal 2023, 2,244 employees of the Kaneka Group participated in safety-related training.
Training Name | Content | Number of Participants | |
---|---|---|---|
Safety Education | HAZOP Training |
|
68 |
Training for dedicated safety technicians |
|
14 | |
Human error prevention and analysis training |
|
10 | |
Chemical Risk Assessment (CRA) Training (explosion and fire prevention module) |
|
33 | |
Chemical Risk Assessment (CRA) training (health hazard prevention module) |
|
35 | |
Comprehensive safety technology training |
|
30 | |
Risk assessment training |
|
29 | |
Plant safety technology training (basic course) |
|
20 | |
Safety experience training (Preventing entrapment and entanglement) |
|
222 | |
Safety experience education (static electricity, explosion, fire) |
|
206 | |
VR safety experience education |
|
1,510 | |
Line manager training | Training for newly appointed manufacturing department managers and manufacturing group leaders |
|
- |
Safety management training for manufacturing managers |
|
24 | |
Safety training for newly appointed manufacturing managers |
|
3 | |
Training for newly appointed group company manufacturing managers on safety |
|
30 | |
Foreman management training: occupational safety and health law training |
|
10 |
Safety Awards
Certification as a Safety-conscious Company by the Japan Chemical Industry Association
Group Company | Certification for Zero Accident and Disaster Period |
---|---|
Kaneka Solartech Corporation | More than 3 years |
Kaneka Tohoku Styrol Co., Ltd. | More than 10 years |
Kaneka Kanto Styrol Co., Ltd. | More than 10 years |
OLED Aomori Co., Ltd. | More than 10 years |
Tamai Kasei Co., Ltd. Plant No. 1 | More than 10 years |
Tamai Kasei Co., Ltd. Plant No. 2 | More than 10 years |
President’s Safety Award for No Accidents and No Disasters based on the Internal Standards (Fiscal 2023)
Group Company | Award for Zero Accident and Disaster Period |
---|---|
Kaneka Medix Corporation | November 9, 2010 — |
Kaneka Solartech Corporation | October 31, 2018 — |
Tochigi Kaneka Corporation | May 26, 2012 — |
Cemedine Co., Ltd. | January 11, 2019 — |
CHECK & ACT
In 2023, 16 occupational accidents occurred. To achieve zero accidents, we will work to promulgate basic safety actions to all employees, improve production line management, and strengthen the risk assessment foundation.